Update #1 Time taken: 0.00
I was going to ask David if he has a pic of the build off knife in a closed position to see what it would look like but then I thought I can use the power of my (not quite a water jet) ink jet printer to print out a copy. Then I can see how things will all line up and how it will look in the hand as well as closed. So here are some pics.
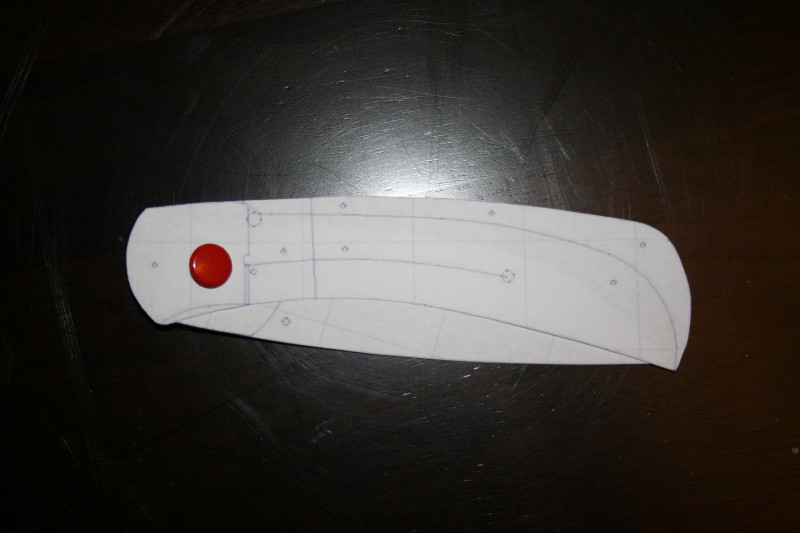
It is a bit bigger than the slip joints I have been doing.
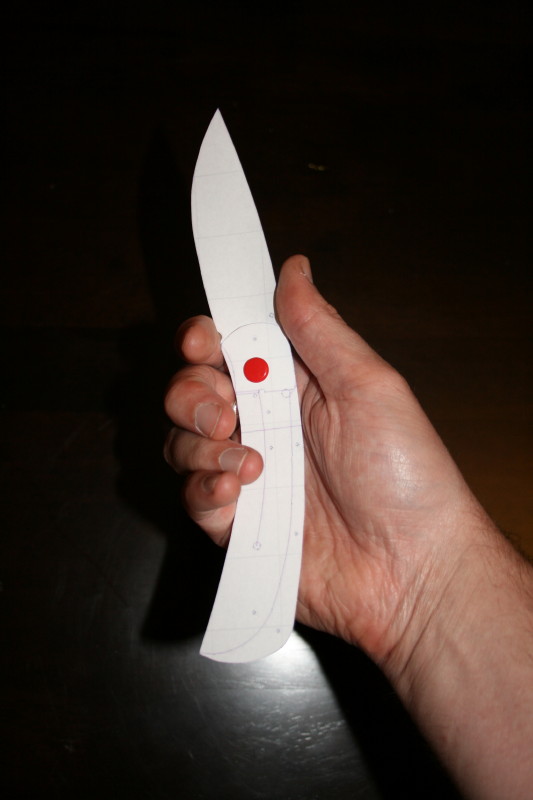
I'll probably start drawing some grind lines on there too see how I am going to fit everything in.
I also started to put together a list of all the drill bits and tools I'll need to put the knife together. Apart from all the usual sand paper and belts etc. This will be the first liner lock I have made and the first time I have used Titanium on a knife.
For the 1/8th pivot pin and stop pin:
- #31 drill bit
- 1/8th reamer
- Step Drill (unknown size)
For the 1-72 screws:
- #52 drill bit (up one size from 53 since we'll be tapping Ti) I'll be using several of these as pins at the same time when drilling the other holes for the 1-72 screws
- 1-72 Tap
- #48 drill for clearance holes
- Counter Sink for flat head screws
- Step Drill Bit (unknown size) for the button head screws.
For the lock:
- Dremel cut off disk (depends how it comes from the water jet)
For the thumb stud:
- All the ones on Tracy's site seem to use 1-72 screws so we should be ok here
For the detent: (I was going to try the same process as described in Ed Caffrey's flipper wip thread here
- #55 drill bit for the hole in the blade
- #53 drill bit for the detent ball to go in
There are a few things there I don't have so I'll have a bit of shopping to do :)
Update #2 Time taken: 0.00
Ok I am going to have some spare time in the shed this afternoon I thought I would try to get everything to the stage where I can see how the knife fits together. I'll be using the back spacer provided so I'll need to drill some placement holes in that. So the plan is
- Grind tabs of blade, liners and back spacer so the tabs don't get in the way when we drill our holes.
- Drill the pivot hole in the blade with a number 31 drill bit
- Ream the pivot hole in the blade
- Drill and ream the pivot holes in both the liners
- With the pivot in in the liners drill one of the back spacer holes. This will be with a number 49 drill bit for tapping to 2-56 later.
- With a drill bit in that hole drill the remaining 2 holes for the back spacer
- Line up the back spacer on one of the liners and drill a number 49 hole in the back spacer
- With a drill bit in the first hole for alignment drill the second spacer hole.
- With the back spacer pinned in place drill the last hole.
- Now we can drill clearance holes in one of the liners and the back spacer with a number 43 drill bit.
- We can also counter sink these holes (must make sure we counter sink the right side)
- Now we can tap the other liner with a 2-56 tap
- Now we should be able to assemble the knife for the first time and have a look at how it is going to work out.
Update #3 Time taken: 0.00
Ok I got a fair bit done today. I am ready to figure out how to proceed from here. Here are some pictures along the way. I also had a few little "issues" that I will let you guys know about so you can see what I did.
The first thing I was going to do was grind all the tabs off the liners, blade and back spacer. I decided to grind all around the back spacer and the blade except for the parts which will affect the fit up of the liner lock mechanism and where the blade sits when it is open and closed. I have marked them in this first picture.
This is my grinder. It is a variable speed RadiusMaster made here in Australia. A very expensive piece of kit but excellent for making folders especially if you have limited space. I have mine on a board with wheels so it can be moved into position under the light when needed and pack away when I am finished so the car can go back in the garage.
Here I am checking to make sure the work rest is 90 degrees to the platen before I grind the outlines down and the tabs off. The RadiusMaster has the platen, 3 wheels up the top, a 4" wheel down the bottom and the big 8" wheels all usable. I'll be using a P100 belt that was handy for doing the profiling.
Would you believe I didn't take any photos of grinding the tabs off. I need a helper photo taker or something. This was the first time grinding Titanium, it has some nice bright sparks doesn't it. I flipped the RadiusMaster on its side to do the inside of the back spacer.
I always check for squareness when I switch work rests.
Here we are after grinding the tabs off.
Update #4 Time taken: 1.00
After any type of profile grinding like this or drilling any holes you will create a little burr that needs to be sanded off. I use a little tab of masking tape to make a little handle to flat sand them on my granite flat (which is actually a granite chopping board). I used P120 to start with on the blade to get rid of the mill scale and P240 on the liners and back spacer. I found that the titanium sands really easily.
The blade was a little bent. It was still ok to sand off it is hard to tell in this photo but there is mill scale in the center section. I wanted to get this side completely flat before I went drilling holes.
Here it is after I drilled the hole with a #31 drill ready for reaming. After each hole I dril I will deburr it quickly on the P240 sandpaper to make sure all the hole I drill are perpendicular.
At this point I realized I didn't have any #49 drill bits to drill the tap holes in the liners or and #43 clearance drills either so I have to run off to the shop before they closed. Luckily it is daylight savings here so I could keep working quite late. That meant I didn't get any photos of the drilling the liners process.
The process I did was this though. On the lock side liner I drilled all the holes with a #49 drill bit deburring as I went when necessary. I then aligned the liners with the pivot pin in one end and clamped them together so I could drill through the lock side liner into my other liner. After the first hole was drilled I used a spare #49 drill bit as a second alignment pin and then went and drilled the rest of the holes. Once that was done I aligned the back spacer with the edge of the liner and drilled my first hole in that. I pinned it with the drill bit again and drilled the second hole. I put another spare drill in that hole and drilled the final hole in the backspacer. Once they was done and everything was deburred I went back and drilled the 3 liner holes out with a #43 drill bit and went through the same pinning and drill process on the back spacer. Now I could tap the 3 liner holes for the lock side liner as well.
It is important to note that although I drilled all the holes for screwing the handle scales and bolsters onto the liner with the #49 drill bit I didn't tap them yet as I will need to drill through them again when we are fitting the bolsters and scales onto the knife and if we had tapped them already we could ruin the liners when we drilled through the tapped holes again.
Here is is before I counter sunk the holes in the liner without the lock. This is where my first gotcha came up. Using a 2-56 counter suck screw there is no a lot of room between the edge of the liner and the screw head. I left about 1/32 between the edge and where the counter sunk starts and I haven't touched the profile of the liners yet I only ground the tabs off. Hopefully I have left enough space so I don't hit the counter sunk holes.
Now for the second gotcha. In that picture you can see how close to the bottom of the back spacer I had to drill the clearance holes so that the top edge was aligned with the edge of the liner. It would be easy to drill them too close so the hole came though the edge. However if you leave too much you'll have to take too much off you liners to get the spacer to line up with them and you'll risk hitting your counter sunk holes.
At his point I decided to drill the stop pin hole while I have the liners together. Easily done with the #31 drill bit and 1/8th reamer. It is a nice tight fit. Now to see how it all fits up together. You can see in this pic the back spacer is blocking the stop pin so I will have to grind that back a bit next time I get into the shed.
Plenty of space for adjustment in the closed position though. You can see how close the counter sunk holes are to the edge in the top liner.
I thought I would remove the back spacer and see how it went against the stop pin now. I'll need to take some off the back of the tang to raise the point up a bit.
Also the bottom corner will need some grinding off as it won't clear the stop pin as it is at the moment. I want to be careful here since it is in the area where the detent ball is I don't really know what I need to worry about with the fit up.
It is hard to tell in this picture but the point of the blade is just outside the liners here. That is ok as there is plenty of room for adjustment and I haven't even began to grind that area of the tang out.
That leaves the to do list for next time as:
- Grind the front of the back spacer down so the stop pin can go through.
- Grind the back of the tang down where it meets the stop pin to raise the point up a bit.
- Grind the bottom corner of the tang off so it will clear the stop pin and the blade can open and close.
- Grind the bottom of the tang down where it meets the stop pin so the point of the knife doesn't protrude.
At this point I am going to think about any changes I might want to make to the blade profile and where my grind lines are going to go. I'll also want to figure out where I am going to put my name stamp.
Update #5 Time taken: 4.00
Managed a bit more time on the build off knife today. I thought I would start with the back spacer thickness. So I got out the micrometer and started measuring.
As you can see the overall difference between the blade + washers vs the spacer is 0.05mm which I am happy with for now. I'll do some fine adjustment after the HT and polishing is done. In the picture you can see I marked the spacer and the corner of the blade so I could scribe in the stop pin hole what would need removing so the knife can go together properly.
There wasn't a real lot that needed taking off the back spacer. On the blade all I needed to remove was the bevel from the waterjet process. Once that bottom edge was cleaned up it passed the stop pin without any problems.
After that I assembled the knife again and ground back the extra thread on the 3 back spacer screws and I also ground down the heads of the screws so they were flat. This is a bit of a worry since there is not a lot of the torx head left once the head is ground down. I stripped the driver inside one screw already luckily we have spares.
I am thinking for my build off knife I will have a hidden pivot pin. So I thought I would start on the bolsters. I would also like to know if I can move the front edge of the bolsters back a little to give a little more space on the blade for my name stamp and keeping a decent blade edge.
First thing I did was grind off the tabs left from the waterjet and then flatten one side of the bolsters so they sit flush against the liners. You need to make a left and a right side one. I lined up the bolster and clamped it on the liner ready to drill the first hole. You could also super glue it on and pop it off once the holes were drilled.
I drilled these holes with a #49 drill same as the holes in the liner. Once the first one was drilled I used a spare drill bit as a pin and drilled the second hole.
I lined up the 2 bolsters against each other and started drilling the holes in the second bolster. Once the first one was done I pinned it in the same way for drilling the matching holes. After each hole was drilled I deburred it to make sure each hole was drilled perpendicular to the liners.
Now the bolsters could be pinned together and I could grind the face of them down where they will meet the handle scales. Now each side will be matching.
The last thing I did was to pin each bolster to the correct side liner and spot where the screw head is going to sit underneath the bolster. I need to figure out how I am going to do this. The screw head itself is just over 4mm across but if I just drill a 4.5mm hole it will go to far into the bolster. I'll probably end up having to get a new end mill bit or something to do a flat bottomed hole.
That is where I have left it for now. I'll wait until I have the bolsters done before I decide if I can remove a bit of the front edge of them and from there if I can re-profile the blade a touch. Another thing I realized today was the because of the liner lock you will be able to see the back side of the bolster and the handle scales. We will have to make sure those sides are cleaned up and polished too.
Update #6 Time taken: 6.00
Ok it has been a little while since I have had a chance to work on the build off knife. I had a knife to finish for a birthday before the end of Feb and I have been getting a bunch of knives ready to send off for HT so I might actually have a chance to finish some of them for the Melbourne Knife Show in May.
Today I spend the last hour in the shed getting the bolsters ready to go onto the knife. First up was milling a space for the screw head to go. I used an end mill for this and then dremelled out the center a touch more so the bolster could sit flat. This was just after I finished one of the bolsters.
and here they both are after the clearance was milled in. In the box you can see some of the knives I have been getting ready. From left to right there is a 2 blade sowbelly wharncliffe trapper, a damasteel and carbon fibre slippie and a screw together construction slippie.
After that was done I drilled out the screw holes on the bolsters with a #43 drill bit for the clearance hole for the bolster screws. Then I tapped all the bolster holes in both liners so I could trial fit them.
I still need to grind down the pivot pin and the stop pin so I can get the bolsters on both sides at the same time. The main reason I have been doing the bolsters was that I wanted to see how the screw head looked on there. I wanted to see if I could shave some off the front to give a little more blade length. I also plan on altering the blade a touch. At the moment it is very "leaf" shaped but I would like to see a bit more of a point on the blade so I'll flatten out the top a bit I think.
Update #7 Time taken: 7.30
I managed to get a little bit more done in the last couple of days. I almost had a disaster on my hands. I was planning to grind some off the top of the blade.
Well after I ground some off the top I thought I would grind some off the back of the tang so it lined up with the top of the knife when it was against the stop pin. You can see in the picture how much the tang was into the stop pin hole.
What I failed to look out for was due to rotating the tip up it would move the bottom of the tang away from the front of the lock face. Fortunately I stopped grinding the area near the stop pin before I reached my scribe marks and the lock [I]JUST[/I] covers the tang. I might still have a disaster on my hands if I can't grind the lock face at the right angle but I am hoping I can stretch the lock out a touch if that happens.
Next thing.. grinding the blade I think I will wait until after HT before I grind the lock face. I must admit I like the look of the reshaped blade though.
Update #8 Time taken: 8.00
We had a long weekend this weekend so I had an extra day to get some knife making done. I have a bunch of knives that are off getting HT at the moment so it is a perfect opportunity to get some time in on the contest knife.
Lots of work ahead of me.
I last left the knife in a worrisome state after mucking around with the blade profile and grinding back the tang where the stop pin hits it. After having a look at it I think it should be ok but the bit where the lock hits the tang might not be as far down on the tang as it would be ideal.
This is where I was up to.
You can see the blade just sits outside the handle before I adjust it. I am only working with the liner and the back spacer here so I can easily see what is going on.
Now after adjusting it the blade sits nicely inside the handle. I just ground off inside the curve with the smallest wheel I have on my grinder using a 240 belt so as not to remove much at a time.
Next I thought I would mark out where my grind is going to go. I drew it on in the open position to have a quick look.
I thought it showed a little too much tang in the closed position so I thought I would adjust it a bit.
Here you can see I have moved it back just a touch. Now I am going to do something a little different again. I thought I would put a nail nick on the knife rather than a thumb stud. This is just my idea of a gentlemen's knife. It shouldn't need to be opened single handed. So I mark a line parallel to the spine where it was going to sit and marked the center of it.
First part of the process is to line up the scribe mark parallel to the top of my vice in the mill.
I then use a drill bit to line up the centre point on the spine of the blade. I then lock the x axis on the mill in place.
This is my fly cutter bit just in case someone wants to know the shape I have ground the cutter tip to.
Next I align the tip of the cutter to the scribe line on the blade. Once that is done I lock the z axis of the mill in place and I am almost ready to get cutting.
I need to know how thick the blade is so I only go half way in. In our case it is 3.2mm so I go in 1.6mm which is one full turn of the y-axis in my mill.
Here is the end result. The nail nick might look a bit wide at this stage but it will narrow down when I grind the bevels on the blade.
Update #9 Time taken: 10.00
Next up is grinding the blade. I have been trying out a jig that was in Chris Crawford's slipjoint DVD. I have marked the edge of my blade with some layout dye and used a drill bit to put the centre line on my blade.
Just about to start grinding. The angle of the jig can be adjusted by screwing the screw in and out. Once the first side is done you can lock the screw in place and then just grind the second side. The little brass bit is to support the blade while I grind it. you can drill different holes depending on the blade shape and length.
Here is the first side ground out. I didn't get much pictures of this process since I am dipping it the water a lot and generally getting messy.
Once I had ground both sides I decided the edge was too thick still so instead of mucking around with the jig I decided to just grind it by hand. This bought the grind up a bit higher on the blade too. This is the nick side after grinding
and the opposite side.
I also ground back the stop pin so it was flush as well and the pivot pin. Now I just need to shorten up some of the screws so I can test assemble it for real.
I am almost ready to HT the blade now but before I do that I was going to drill the detent in the blade. Having never done a liner lock before I am going to go back and read Tom Anderson's tutorial again as well as Bob Terzuola's book. The element in our oven broke last week as well so I can't HT any blades until it is fixed and I can temper them again so it will give me a little time to read up on it.
I am also trying to decide if I should clay coat the blade for HT. Since we are using 1095 it is possible to get a hamon. Obviously the tang still needs to be hardened but I have some satanite so I could give it a go. The other option is just a nice hand rubbed finish.
Update #10 Time taken: 11.30
I found out that there is a local knife maker that has an anodizer I can use so this has changed my mind a little on what I am going to do. I had a piece of mokume laying around from an older project that I never used it on. I think now might be a good time to use it so I spent the first part of the day matching the holes in the existing bolsters and fitting up the new mokume bolsters.
The next thing was to fit the handle scales as well. I cleaned up the front edge on the grinder. A nice trick for this is to do the bolsters facing with the top facing up and the scales with the top facing down. That way if your work rest isn't exactly 90 degrees to the platen you will still get a seamless join. With that done I drilled through the liners with a #49 bit with the scales clamped in place.
Once that was done I tapped the last of the holes in the liners and drilled the scales out with a #43 clearance drill bit. In order to get the blade ready for HT I also hand sanded it with P240 sandpaper. I like to do my first hand sand before HT just in case there are any trouble spots it is a lot easier to get them out while the steel is annealed.
In order to put the knife together we'll all have to shorten the screws. I used my grinding jig to to this. I just put the screw coming out the front and ground it down. It was very easy, plus I like this photo for some reason. It is the view I have when grinding :)
I thought I would do a trial fit now. You might notice something else new apart from the mokume bolsters. I was looking at the usaknifemaker website and saw that they had some lanyard beads that just seemed like they belonged on a knife that would be raffled off to start a knifedog's charity. I am just hoping it turns up before the end of the build off.

So now you can see the addition of a lanyard hole in the back of the knife. That meant drilling a bunch more holes and tapping another screw hole.
Next up was grinding the profile of the handles. I was being really careful here not to go into the countersunk holes on the liners since they are so close to the edge. I pulled the scale off several times to check how much material was left. I didn't get much photos of this bit since it is a bit more dirty work so I put the missus to work with the camera. Trying to keep up safety message since I am grinding micarta I have the respirator on and the hearing protection and my leather apron. I just hope no one notices the face shield in place on the wall :p.
While I was there I started rounding off the edges on the handles. I won't finish those off until I have counter bored the holes for the screws to go in in the bolsters and the scales. It is starting to look a bit more like a knife now.
The last thing to do before I can HT the blade is to drill the spot for the detent ball to sit in. I have never done this before so I checked out a few other tutorials and wips and went with the drill through the liner method. I used a #55 drill bit first to go through into the blade then disassembled everything and drilled the liner with the #53 bit. I spent a bit of time trying to figure where to locate the hole. I think I might have been a touch conservative on this one. I could have gone a bit closer to the edges by a touch.
That is where I got up to. I also counter bored the holes in the bolsters and handle scales. Everything is ready now for HT and rounding off the handles. I'll HT the blade one night this week and hopefully I'll have the knife finished next weekend. The last blocking point for me is fitting up the lock since I have never done that before. I'll have to get a piece of micarta or something and grind a 7-8 degree slope on it to use as a rest for grinding the lock face.
Update #11 Time taken: 16.00
While the blade is in the oven tempering I can post what I do for the HT process.
This is my HT setup. I use the forge that a few other knifemakers and I spent a weekend making. In the end 4 of us made 7 forges so we could sell the extra 3 to fund all the materials for all the forges. I have a little speaker magnet on the side of my cart so I can test for the point where the blade goes non magnetic.
For my quench I have a container of olive oil I use to quench in. I just opened the top with a can opener. For my folder blades I use an old steel coat hanger to go through the pivot hole and I bent it around so the tip of the blade is supported too.
The actual HT process I do is to put the blade in the forge for a 10 count. I keep doing this until I start to see the blade starting to glow a dull red. At this point I reduce my count to a 5 count and start to bring the heat up. I quite often let the blade cool down a bit out of the forge before I hit the critical temp to allow the heat from the outside of the blade to warm the middle of the blade. Since the tang of the folders needs to be hard for the lock I try to keep the tang in the hottest part of the forge. The edge will heat up to critical temp first anyway since it is the thinnest. We just need to make sure it doesn't get too hot. My goal is for the blade to be a completely even colour as I take it past critical. Once I am at a medium to bright red I start to check for the non magnetic point. Once it hits the non magnetic point I will start to look for the changes in the colour of the steel that means we have reached critical. At this point I am only holding it in the forge for a 2 count max and quickly taking it out, inspecting the colour and back in to heat it a small amount more. When it reaches critical point it will seem like the colour refuses to change like the steel isn't taking any more heat then all of a sudden it will jump up a much brighter colour red. I try to keep it at this point for a little longer to make sure the blade is completely heated through. The final heat before I quench I look for the quench container and leave it in there for a couple more seconds than I have in the previous heats and then as quick as I can I take it from the forge into the oil with the tip straight down.
This was the first time I have used 1095 before so I was very interested to see how it went. I found it much easier to tell the critical temp on the 1095 versus the O1 I have been using. I when I reached it I could see a ring of the below critical temp in the middle of the blade and it gradually expanded to the edges as the blade cooled. I knew I was really close then.
I was taught to look for the changes in the steel by Shawn McIntyre at a bladesmithing symposium/hammer in. Once he explained it my HT improved by 200%. A way to train your self to see the critical temp point is quite easy. If you put a bar of steel in the forge and leave it until the tip is really hot. As it cools down the coolness will generally come down from the end you are holding towards the tip. As it cools you are looking for a dark band the will go down the bar. In front of that band the steel is above critical.. behind it the steel is below critical. He basically explained it as at that critical temp point you need to put in a lot of extra energy into the to free the carbon atoms from their bonds with the iron to go into solution with the iron or something like that at least. I am not a metallurgist.
I also noticed that we have reached a milestone of 1000 views of my build off thread. Thanks for looking everyone. Not too many pictures in this update but hopefully you found it very useful and informative.
Update #12 Time taken: 17.00
Well this week has not been a very good week for me at all. Started off by getting hit by a car whilst riding my motorbike to work. Then had quite a bad experience with a supplier which I am not going to go into but has left a very bad taste in my mouth. Then I was tempering the build off blade in our oven. It has just had the element replaced so the temperature in it has gone up and it got tempered at too high a temperature.
Normally you would expect a nice straw colour but the rear on the blade has gone past that colour and is a dark purple so now I am going to have to HT the blade again.
The important lesson for everyone here is too make sure you have a clean surface to gauge how the temp went regardless of how many times you have tempered blades before. If I hadn't done that I wouldn't know that the blade was now too soft.
Well just because I can't work on the blade doesn't mean I can't work on the build off knife. I decided to do some work on the handle. When I left it I had ground some bevels around the edges on the handles to get ready for slack belt grinding to round them off. This is where I go up to after the slack belt grinding. I started with a 60 grit belt going perpendicular to the handle then switched to the 240 grit belt to smooth things right out and get rid of all the deep scratches. I did this at a 45 degree angle so all the scratches show up easily.
After that I started hand sanding, starting with 240 grit again. The hand sanding makes a big difference I think. The dark spot is a bit where the micarta was still wet.
You can really see the pattern in the mokume start to come out now.
After that I started to clean up around the lock on the liner. I used an old 240 belt that I had blown out one of the edges on and split it in half. I got this in the gap between the lock and the liner and carefully ground out all the water jet marks. As a suggestion it might be nicer on future version of the kits to make this gap just a touch wider so it can be hand sanded a bit easier. While I was at it I ground an area on the opposite liner to allow a little easier access to the lock.
The list of things to finish off on the knife is gradually getting a bit smaller.
- HT the blade again
- Hand sand the blade up to a nice hand rubbed finish. I am thinking of taking it up to 1200.
- Thin out the back spacer so it is the same width as the blade and 2 washers.
- Finish sanding the back spacer (and anodize it maybe)
- Finish sand the liners and anodize them gold
- Hand sand the handle material up to 600 or so and then buff.
- Hand sand the bolsters up to 600 or so and leave them a satin finish so the mokume stands out better.
- Fit up the lock and install the detent ball.
- Grind down the gold screws to length.
- Make the lanyard for it once the bulldog bead arrives.
I also picked up an oven thermometer today :)
Update #13 Time taken: 20.00
Just a quick update I re did the HT on the blade tonight. Checking the oven temp with my new oven thermometer. It had it warming up at 210C(~400F) and the oven thermometer was reading 240C(~475F) so you can see why it went way too far last tempering cycle. I have it going at 180C now which is sitting on 205C(400F) hopefully it stays stable at that for the next 2 hours.
Update #14 Time taken: 21.00
Well it is pretty much complete now. I didn't take so many pictures today as it was mostly just hand sanding. First thing I did was grind the scale off the blade and mark the position of the lock face.
That piece of g10 you can see I have ground a 7 degree angle on for the blade lock.
Before grinding the ramp for the lock I bent the lock out and fitted the detent ball in place. Here is the closed blade. The detent ball fits very nicely holding the blade closed.
You can see inside the area where the lock ramp is I haven't been able to grind all the way down. There is a black section there due to mucking around with the top of the blade. It still locks up though just not ideal.
And here it is open with the lock in place. If you open it by hand the lock comes in by about that amount. If you flick it open from half way the lock engages further but it gets very sticky and hard to unlock. Not sure what I can do to fix that.
At this point I was ready to do all the finishing work on the blade. I had dirty oily hands so no photos taken during this process.
After a big pile of sandpaper bits this is what we are left with.
Since then I have etched the mokume bolsters and made up the lanyard. The knife turned out great. I just need to figure out if I can do anything to fix the sticky lock and I'll be done. If anyone has any fixes I can try out please let me know.
I'll get some better photos with the lanyard on there in better light tomorrow.
Update #15 Total Time taken: 24.00
Ok finally got a nice day when I had some time to take some pictures. I really need to get a better photography system set up. I have some little boxes I had laying around as well so I thought I could put one to good use on this project.
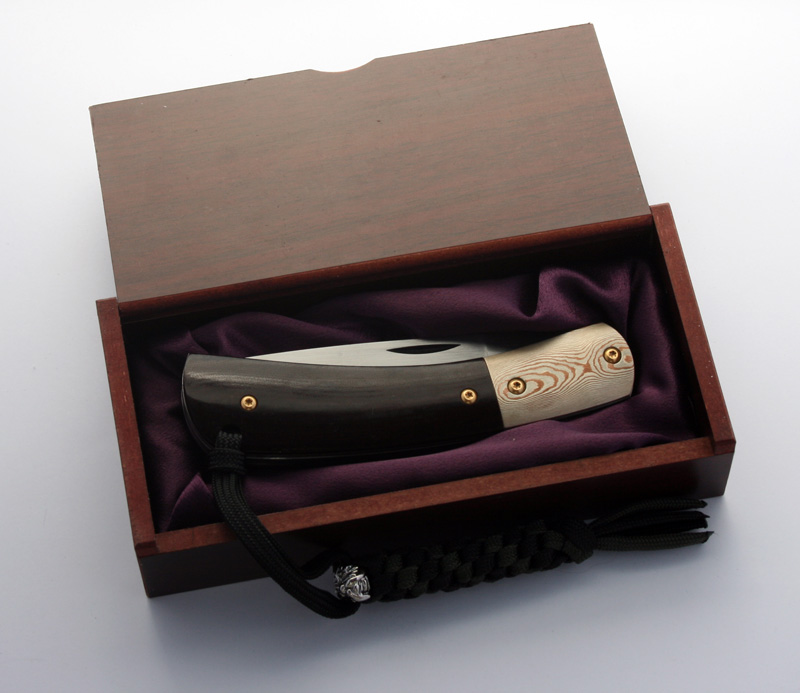
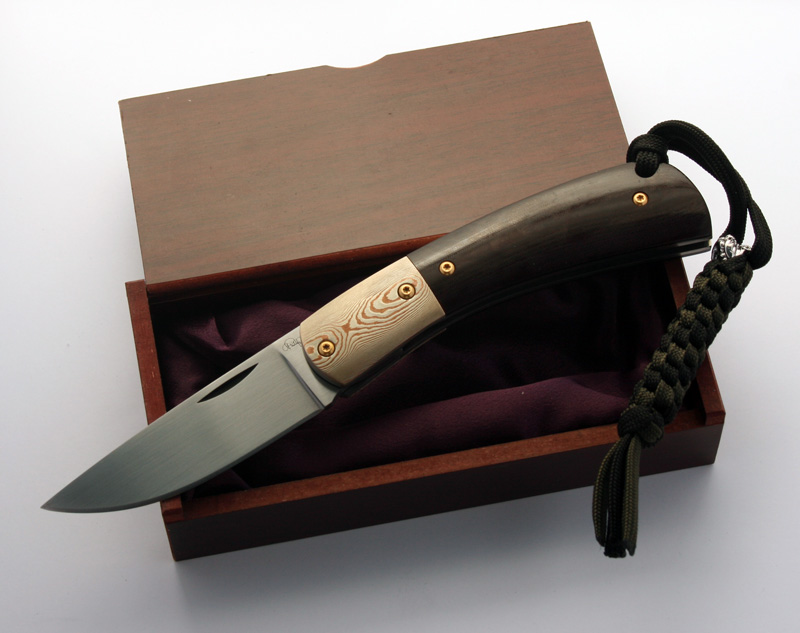
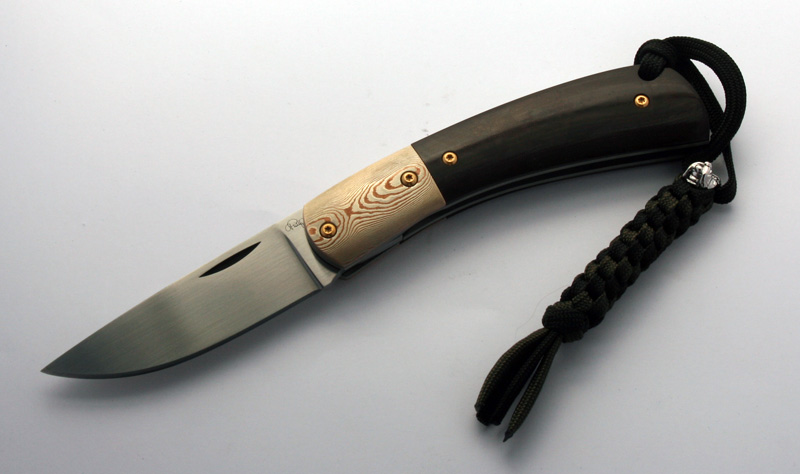
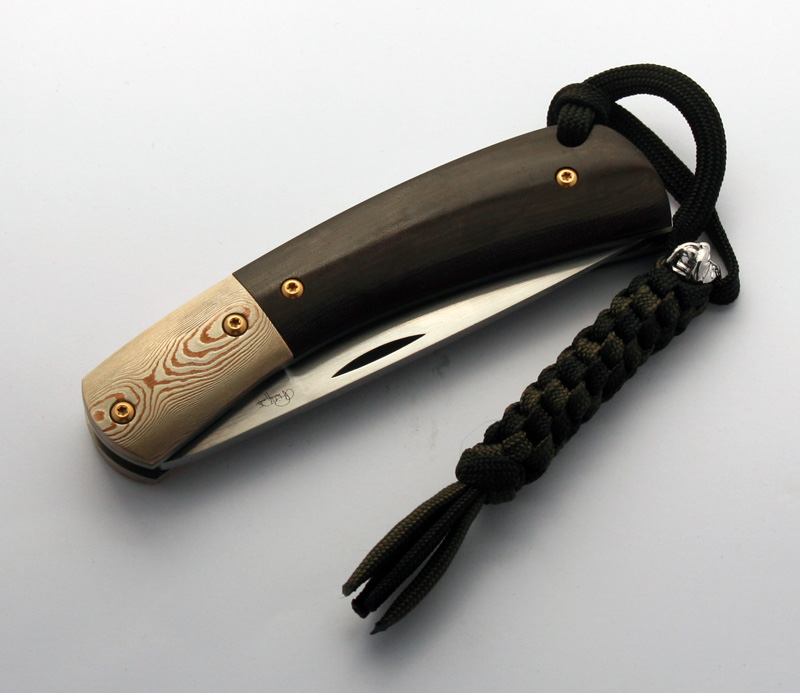
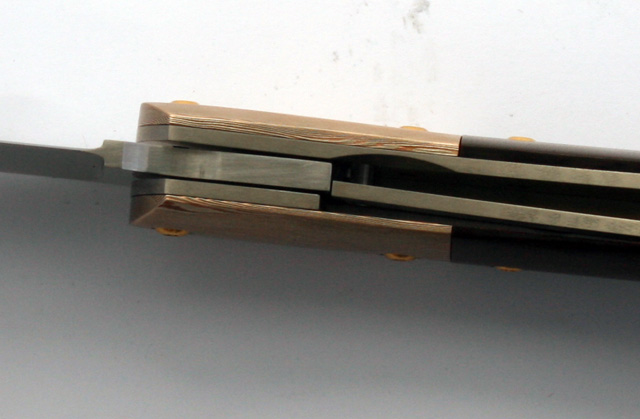
I have really enjoyed making my first liner lock. The experience was very different to the slipjoints I have been making. I hope everyone has enjoyed the process as much as I have.. Now when is the next build off?